
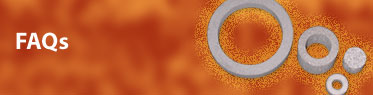
Frequently Asked Questions
What is Bubble Point Testing and Micron Grade?
This test is a common industrial test for estimating the maximum pore size of a material. A test piece is submerged in a wetting fluid such as isopropyl alcohol and a gas pressure until a bubble forms and breaks away from the porous surface. ASTM E-128 and ISO 4003 detail the test method that use Darcy's Law to correlate between bubble point pressure value measured and the calculated maximum pore size. This calculated maximum pore is then multiplied by a pore shape correction factor to estimate the filter rating, also known as the "Micron Grade" for rating our products.
Each industry can use a different shape correction factor, so there are differences in each manufacturer's specifications and bubble point ranges for assigning the "Micron Grade". Several different shape correction factors have been developed for calculating the maximum pore size values, depending on the type of porous material being tested since the nature of the pore changes for different materials. For example, a pore shape correction factor of 0.33 may be used for irregular shaped pores, whereas a correction factor of 0.25 might be used for more rounded pores.
There is a difference between the bubble point values reported on the inspection report and the test results values. We normally subtract one inch of water from the measured value to allow for the back pressure correction. Since the parts are submerged in the IPOH test fluid to one inch below the surface of the fluid bath, the fluid bath generates one inch of water back pressure. The measured bubble point pressure value must be reduced by one inch of water to report the true pressure value.
How do I clean Porous Sintered Metal?
Cleaning of porous sintered metals can allow reuse in some applications where the cost savings can justify the cleaning expense. The cost of disposable of other types of paper or plastic media can be expensive. The lower strength, limited temperature capability and minimal corrosion resistance of most disposable media limits the practicality of cleaning. In order to extend the service life, blocked porosity can be opened with a variety of cleaning techniques and solutions, depending on the nature of the material in the pores. Thermal burn-off, ultrasonic cleaning, reverse flow and chemical processing are typical cleaning methods. Cleaning can often be accomplished with mild detergents, caustic solutions or diluted acids but testing is required to insure that the base metal is not affected. In order to avoid corrosion or cross contamination, the cleaning solutions must be flushed out under pressure and dried thoroughly before being returned to service. Test methods such as visual inspection using magnification, bubble point testing and permeability testing are often performed to determine the effectiveness of the cleaning method. Cleaning methods that mechanically close off or smear the pores, such as wire brushing or sand blasting should be avoided.